五轴联动叶片加工中心做为高端数控加工设备,具有自动化程度高、加工效率高、加工精度高等特点,主要用于汽轮机、航空发动机、鼓风机、轴流压缩机等设备的核心部件叶片的加工制造。汽轮机等设备效率的高低,很大程度上取决于叶片型面的设计和制造水平。
随着电力、能源、航空航天和国防工业的高速发展,汽轮机、燃气轮机厂家的产能将进一步扩大,高端的叶片加工设备需求量也将大幅度增加,高端的五轴联动叶片铣削设备的需求也会有大幅度的增加。发展国内优良品质的五轴联动叶片加工中心,降低叶片加工机床的成本,满足叶片行业生产的需要,是整个叶片行业的迫切要求。
1. 五轴联动叶片加工中心
五轴联动叶片加工中心是加工汽轮机叶片、航发叶片等的关键设备。目前,国内的航空航天发动机厂、汽轮机厂以及叶片专业生产厂,使用的大多是进口五轴联动数控叶片加工中心,叶片的精加工市场完全被国外机床厂家所垄断。由于五轴联动叶片加工中心的特殊性,国外的五轴联动数控叶片加工中心价格贵得惊人,机床的维修费更是令用户难以承担。遇到国际形势紧张的情况,更有被封锁的可能。因此,急需开发新一代的高品质、能够与国外高端产品竞争的国产五轴联动叶片数控加工中心,以打破国外对该类型产品的垄断格局,使国内叶片加工设备逐渐实现国产化,降低叶片加工企业的设备投入成本。
如图1~图4所示,国外生产五轴联动叶片加工中心的厂家比较知名的有:瑞士的斯达拉格-海科特(Starrag Heckert)、利吉特(L i e c h t i)、意大利的法拉利(C.B.Ferrari)和德国的哈米勒(Hamuel)等。国外五轴联动叶片加工中心的共同特点是A、B轴普遍采用力矩电动机,刀具主轴采用电主轴结构,刀具最高转速在12 000~20 000r/min之间,甚至更高,刀具接口以HSK-A63居多;各直线轴快移速度在20~50m/min,以30m/min、40m/min居多。刀具主轴的刀尖普遍处在B轴的回转中心上或其附近,以提高工件表面加工质量,减少B轴所承受的切削力扭矩。而且普遍配置U轴以增加加工范围,A轴头尾架可同步双驱,增大扭矩同时减小叶片加工的扭转变形。
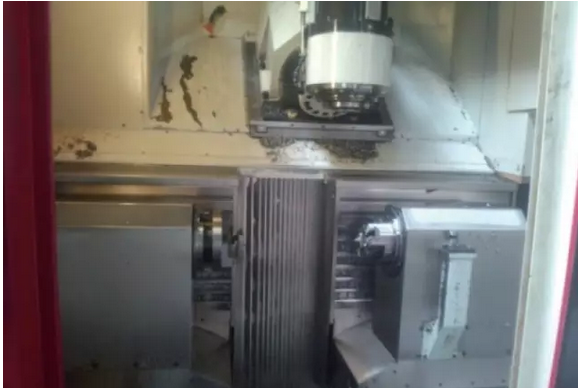
图1 瑞士斯达拉格(Starrag)-海科特五轴联动叶片加工中心
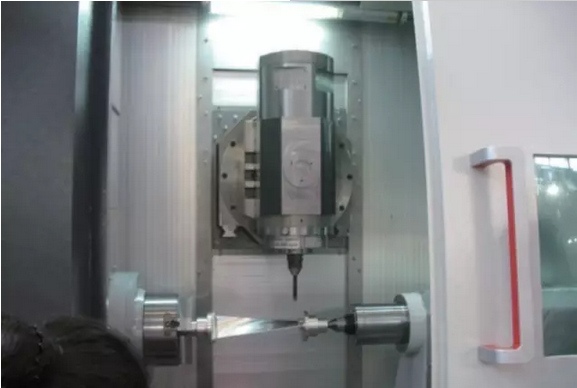
图2 瑞士Liechti利吉特(金切侠注:现已被GF收购)五轴联动叶片加工中心
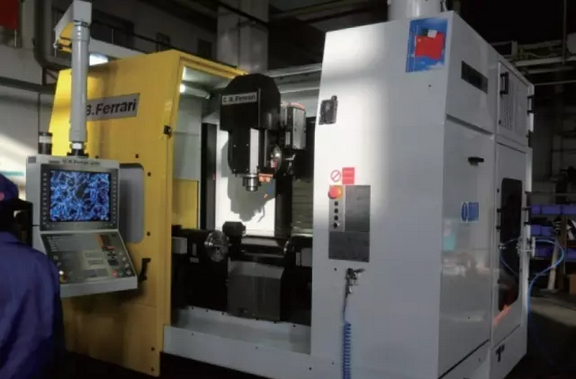
图3 意大利法拉利(C.B.Ferrari,已被中国京城机电控股收购)的五轴加工中心
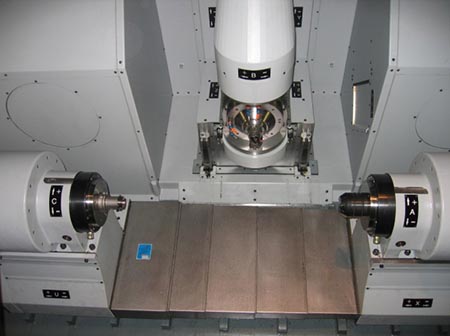
图4 德国的哈米勒五轴联动叶片加工中心
国内五轴联动叶片加工中心起步较晚, 生产该类型机床的主要有北京机电院机床有限公司、新瑞机床(集团)有限公司、四川长征机床集团有限公司和大连科德数控有限公司等。国内五轴联动叶片加工中心有北京机电院机床有限公司的XKH系列、四川长征机床集团有限公司的LVC系列五轴联动叶片加工中心、江苏新瑞机床(集团)有限公司的V5X1800五轴联动叶片加工中心和大连科德数控有限公司KTurboM3000五轴叶片铣削加工中心等。
北京机电院机床有限公司是国内第一家成功研制五轴联动叶片加工中心的厂家,其XKH系列机床是北京机电院机床有限公司在引进技术的基础上,应用国外成熟技术,结合叶片零件特点,自主设计开发的专业叶片加工机床,最大加工叶片长度可达1 600mm,已成功在国内实现批量应用,用户包括东方汽轮机厂、无锡叶片厂、黎明发动机公司等主机厂,以及为主机厂进行配套加工的专业叶片加工厂。
XKH系列叶片加工中心采用立柱移动结构,五轴联动,所有坐标全闭环控制,刀具通过立柱、滑板等部件实现X、Z轴运动,A轴采用力矩电动机直接驱动,响应速度快,无传动间隙,带动工件进行回转,可实现叶片的高速、高精加工,也可以选配蜗轮蜗杆结构驱动;B轴采用优化“刀心距”结构,轴线偏离刀具主轴端面,而与刀尖部位基本重合,偏摆力矩由弹簧平衡装置平衡,驱动有力矩电动机和蜗轮蜗杆两种形式可供选择;工件A轴尾架可以根据加工不同叶片的大小左右沿U轴移动,U轴移动有手动和伺服电动机驱动两种形式,并能够实现工件夹紧后尾架液压锁紧,保证加工精度。适用于由高强度钢、不锈钢、高温合金、钛合金等难加工材料制成的,具有复杂空间型面、薄壁易变形结构的汽轮机、燃气轮机、航空发动机动、静叶片及各类窄长形特殊型面零件的加工,在能源、航空等领域已实现批量应用。图5所示为XKH800Z五轴联动叶片加工中心的实体图与结构图。
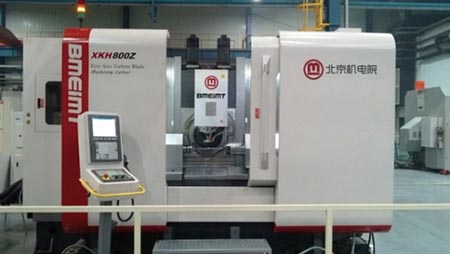
(a)XKH800Z五轴联动叶片加工中心实体图
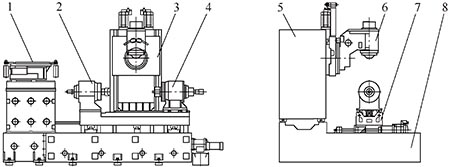
(b)XKH800Z五轴联动叶片加工中心结构图
图5 XKH800Z五轴联动叶片加工中心
1.刀库 2.头架 3.B轴箱体 4.尾架 5.立柱 6.主轴箱 7.工作台 8.床身
2. 叶片自动生产线
随着“工业4.0”和“中国制造2025”的提出以及新技术的发展,叶片加工自动化程度也越来越高。叶片加工自动化程度对叶片加工效率和加工质量起着重要作用。
叶片加工自动化是运用先进工艺技术的基础上,采用现代的机械化、自动化技术,采用自动装置和设备使叶片加工在最有效的状态下自动运行,来加快生产投入物态变换和流动速度,使加工操作的程序编排、生产技术工作、计划、调度以及经营管理等方面的信息进行采集、存储、交换、处理和传递,从而实现生产出的叶片综合效果为最佳的目标,使生产厂能更圆满的达到适应时常要求、为社会服务、有效的增加厂家收益的目的。
叶片加工自动化的意义和效益是巨大的:①提高设备利用率。这是由于加工时间或辅助时间减少的结果。国内目前大部分独立的叶片加工机床的利用效率在30%~40%之间,一些采用自动化生产线的国外机床利用效率能达到70%以上。②降低产品的成本。这是由于产品废品率的降低和设备生产率的提高,中间储备的减少,输送路线的简化以及员工的减少,厂房面积减小以及生产调度简化等。③改进产品质量。这是因为减少和排除了人为因素的影响。④减少了大量的工人。这是由于采用自动设备,实现多机管理,甚至无人生产。⑤从根本上改善劳动条件,减轻生产伤害。⑥提高企业形象,增强企业竞争力。此外自动化生产要求工人掌握更高的技能,可缩小体力脑力劳动间的差距。
国外能够实现自动上下料的五轴联动叶片加工中心生产厂家不是很多,目前只有意大利法拉利和德国HAMUEL公司生产带工件自动上下料生产线。从国内看,只有北京机电院机床公司开发出了五轴联动叶片加工中心生产线(见图6)。
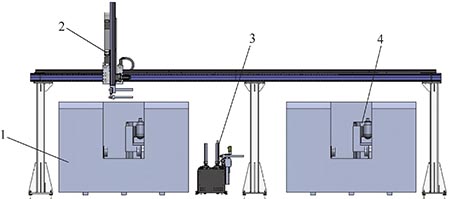
图6 五轴联动叶片加工中心生产线
1、4. 叶片加工机床 2. 桁架机械手 3. 料仓
摆放方式每两台机床构成一个自动生产线,中间设有料仓,料仓循环传动采用链条形式,驱动形式为伺服电动机驱动,为节省空间,工件在料仓中的摆放姿态与抓取姿态成90°形式,料仓上附带一个伺服驱动的手爪及摆缸,为机械手上料做准备,料仓形式如图7所示。
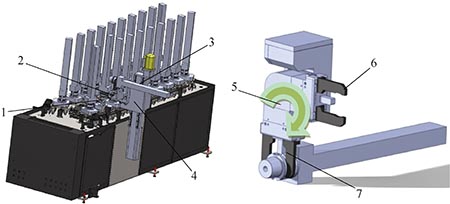
图 7
1.辅助手抓 2、5. 摆动缸 3. 上料姿态 4. 辅助机械手 6. 下料手抓 7. 上料手抓
桁架机械手臂给机床上下料过程为:机械手臂沿X轴负方向(即向左)移动至左边机床上方,等待机床加工完成。当机床加工完成后,自动顶门打开,发出信号呼叫机械手臂换料。机械手臂的Z轴向下移动至程序设定位置(即机床主轴中心位置),下料手抓夹紧, 然后机床夹具松开。机械手臂向X轴正方向移动,使随行夹具完全脱离机床主轴。机械手臂摆缸摆动90°,使上料手抓向下。然后,机械手臂沿X轴负方向移动,使随行夹具进入机床主轴,然后机床夹具夹紧,机械手臂上料手抓松开。Z轴向上移动至机床上方,机械手臂发出信号,通知机床完成上下料,机床顶门关闭进行加工。机械手臂的摆缸摆动90°,使下料手抓向下。然后机械手臂向X轴正方向移动至辅助机械手上方,继续与辅助机械手换料的动作。
机械手上料后, 头尾架配合机械手运动实现工件则自动夹紧,定位,能够实现一次装夹,完成包括型面、凸台、叶冠和叶根圆角等多个空间曲面的加工,同时为了提高叶片加工精度,满足叶片加工工艺要求,通过对尾架移动进行伺服控制可以实现叶片粗、精加工过程中对工件夹紧力的调整。
3. 结语
随着电力、能源、航空航天和国防工业的高速发展,汽轮机、航空发动机厂家的产能将进一步扩大,高端的五轴联动叶片铣削设备的需求也会有大幅度的增加。发展国内优良品质的五轴联动叶片加工中心,降低叶片加工机床的成本,满足叶片行业生产的需要,是整个叶片行业的迫切要求。
叶片加工自动化很好地解决了叶片批量生产的质量和效率问题,在生产中取得了很好的效果。
-End-
金属加工原创,转载请注明
作者:中航国际航空发展有限公司 韩庆元
本文发表在《金属加工》(冷加工)2016年15期65-67页