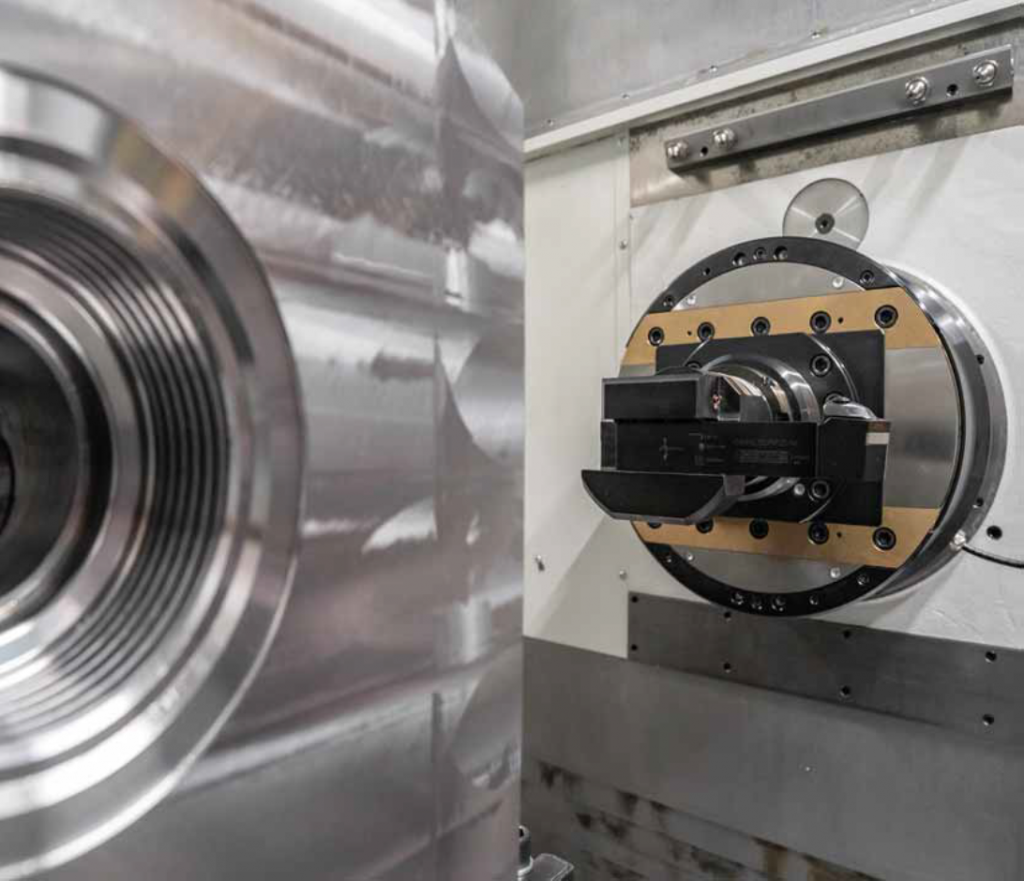
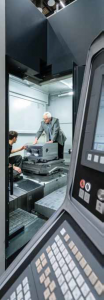
毫无疑问,石油和天然气公司通过使用斯达拉格集团海科特DBF卧式加工中心,可获得巨大利润。这得益于机床采用配备了斯达拉格DBF多任务主轴头的整体U轴,其一次装夹、多面加工的回报是无与伦比的!
DBF主轴头包括一个集成的工作主轴,该主轴为U轴配备了CNC径向面滑板。在车削固定工件时,旋转车刀的轴向跳动仅为5/6微米,可以径向调整+/-35mm。除了车内外圆和端面外,由于径向面滑板带有全行程驱动轴,主轴头还可以车圆锥和轮廓。与 其它U轴刀具附加装置不同,DBF提供12000rpm、45KW的连续功率和1700Nm的连续扭矩,使U轴能够高效且高精度地进行粗加工和精加工。
铣削和钻孔时,工作主轴布置在U轴中心位置,能够输出3500rpm、45kW的连续功率和1700mm的连续扭矩。当不需要U轴时,允许机床作为卧式加工中心进行有效的粗加工和精加工。
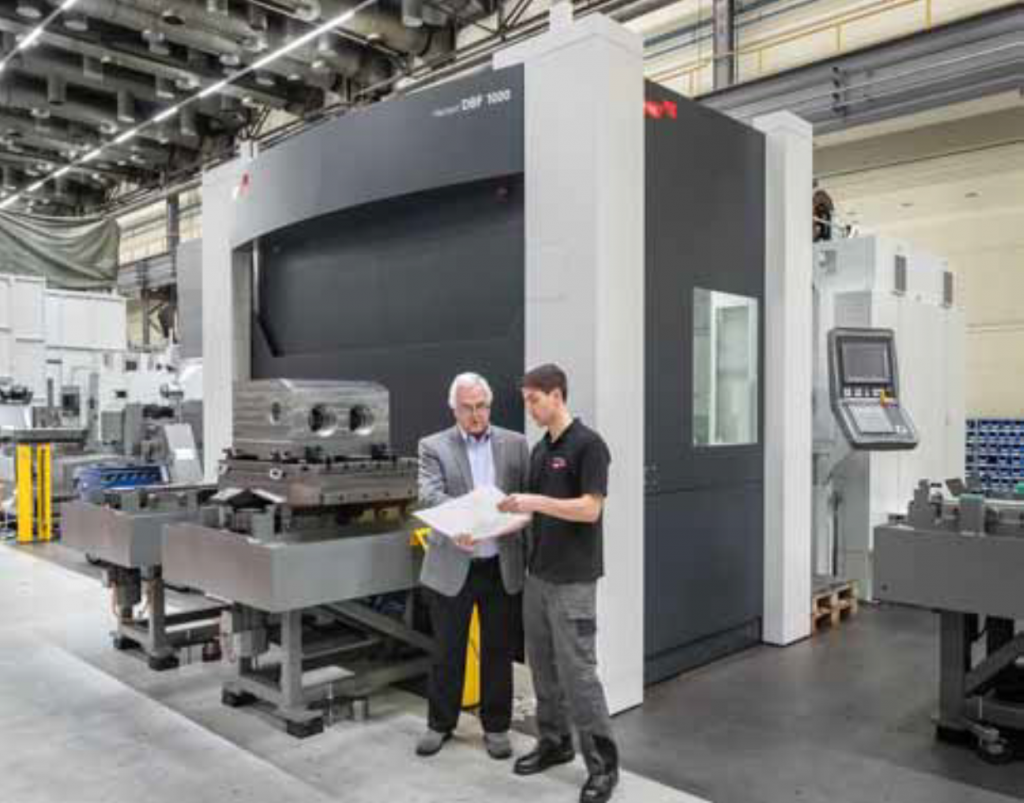
加工节拍减少77%
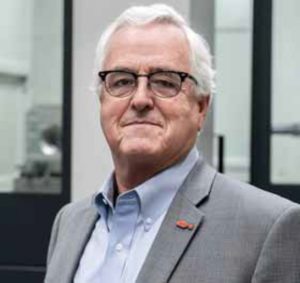
例如,利用DBF机床单次装夹的能力,对流体端、闸阀、钻头和泵壳进行磨削、钻孔和车削,用户 已经能够大幅缩短加工实践。比如,控制阀上的加工时间从20小时缩短至4.5小时,加工节拍减少77%,总加工时间减少95%。
当机床配备了六个托盘的直线存储系统和320把刀具的ATC刀库时,根据工件重量,DBF 1000加工中心是流体端加工的理想选择。凭借其无人值守的特点,以5000mm/min的进给速度使用125mm直径的刀具进行不间断面铣;使用50mm直径的刀具进行立铣;使用70mm直径的刀具进行实心钻孔,然后使用直径89mm的车刀和直径300mm的外圆车刀进行车削。
采用斯达拉格IPS的“工业4.0”解决方案
当斯达拉格IPS应用于集成了直线托盘系统和复杂且高度智能的软件程序的全自动系统时,可创建高性能制造单元,实现最大程度的自动化和最小的操作员。这些“工业4.0”解决方案由斯达拉格IPS(集成生成系统)提供完美的支持。
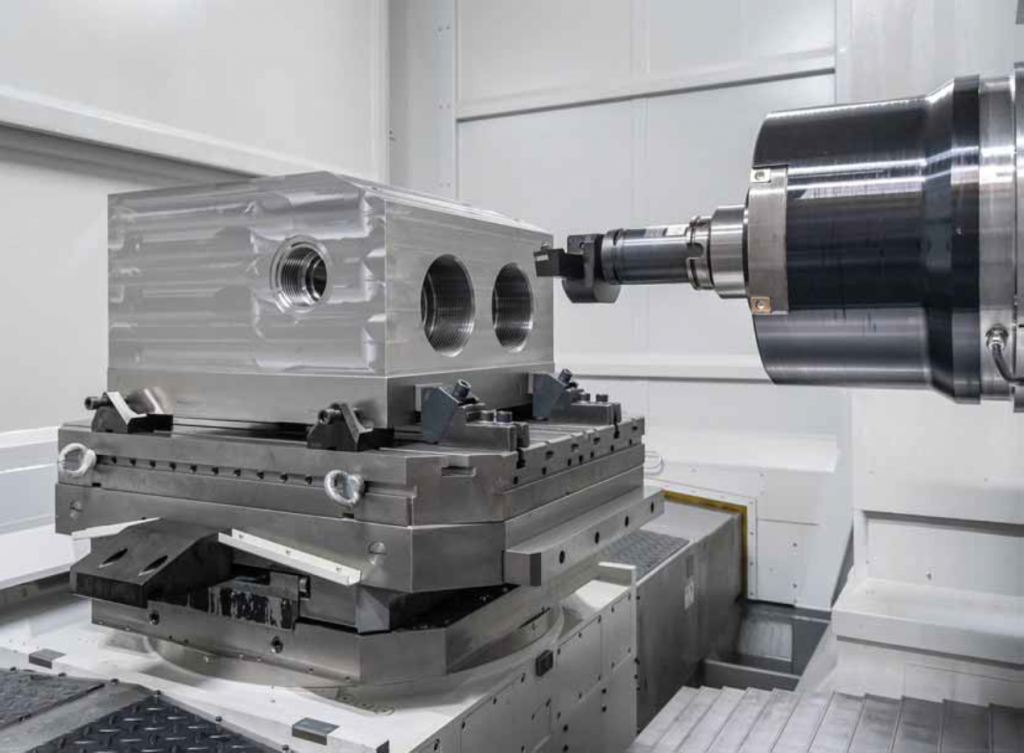
另一个例子是平均寿命为2000/3000小时的流体端的生产,DBF模块可将4吨的实心不锈钢块在32小时而不是50小时内完成加工。加工时间减少36%。海科特DBF 5轴机床系列(6轴加工-无轴插补-添加倾斜数控转台时,无需复杂的夹具)成功的秘诀在于配备了斯达拉格DBF加工主轴头的整体U轴,该加工头允许在U轴和“标准”卧式主轴上进行粗加工和精加工。此外,机床延长了Z轴行程,为进行所需的深孔钻孔(例如在流体端)提供可能。
因此,这些轴的性能使流体端能够从粗加工到精加工的成本效益和效率均得到提高。
精度仅为5-6微米
DBF机床轴的性能为工件每个面(夹紧面除外)的多面(内部和外部)加工提供了无与伦比的灵活性。轴向跳动精度仅5-6微米,所有公差和同轴度无论加工应用的 范围和复杂性如何,始终保持一致。
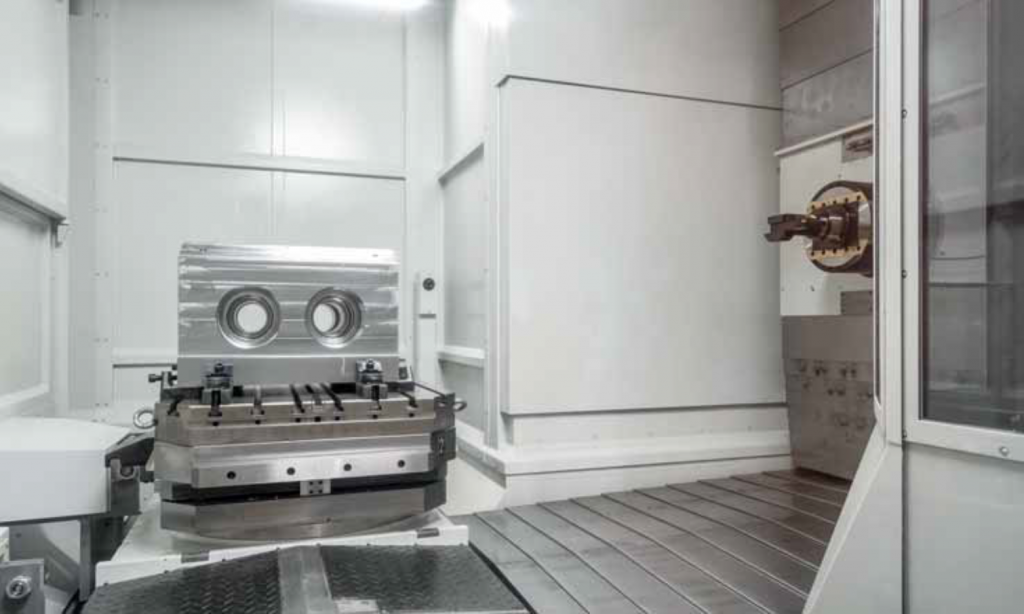
“与通过换刀装置提供平旋盘的其它机床相比,集成DBF主轴使用行业标准刀柄,如HSK 100和Capto,从而允许DBF刀头用户购买标准刀柄,以涵盖所有最高可达500mm的车削尺寸,而不必每70mm行程,就需要一个新的平旋盘。”斯达拉格美国销售副总裁Doug Henderson说。
“于是,当使用集成U轴时,刀尖更接近主轴轴承,刀尖的刚性更大,加工精度更高。此外,集成DBF主轴的扭矩和功率可使加工效率最大化。”
DBF已经取代了两台粗加工机床和一台精加工机床
Doug Henderson补充道:“当然,DBF的一体式工艺消除了单独的粗加工机床和精加工机床(在一个案例中,一台DBF机床就取代了两台4轴粗加工机床和一台4轴精加工机床)的需求(和费用),以及工件重新定位的额外时间和潜在的不精确性。这是斯达拉格哲学“精准开发,想您所想”的完美实践。无论是独立的还是高度自动化的斯达拉格DBF解决方案,都能提供最高的产能、卓越的表面质量和精度。”
原文链接:https://www.jinqiexia.com/products_news/cuttingtools/%e5%8d%95%e6%ac%a1%e8%a3%85%e5%a4%b9%e8%8a%82%e7%9c%81%e7%9f%b3%e6%b2%b9%e5%92%8c%e5%a4%a9%e7%84%b6%e6%b0%94%e9%98%80%e9%97%a8%e4%bb%a5%e5%8f%8a%e6%b5%81%e4%bd%93%e7%ab%af%e7%9a%84%e7%94%9f%e4%ba%a7/