山特维克可乐满位于瑞典基默的刀具生产工厂已被世界经济论坛认定为先进的工业4.0设施。
山特维克可乐满位于基默 (斯德哥尔摩以北) 的刀具生产工厂是一座充分利用数字连接制造的诸多好处的高度自动化工厂。世界经济论坛最近承认了这一点,宣布基默工厂为其全球“灯塔”工厂之一。每个灯塔都是根据在采用数字技术和展示实际利益方面的成功经验,从一份面向1000多个制造单位的调查中选出。
根据世界经济论坛,基默工厂通过其生产流程创建了一个数字主线,大大提高了生产率。一个例子是允许自动改变设计模式 (即使在无人值班时也是如此) 的‘无接触转换’。这样的先进技术意味着基默工厂将成为全球灯塔网络的一部分,从而敞开大门,与其他制造企业分享知识。
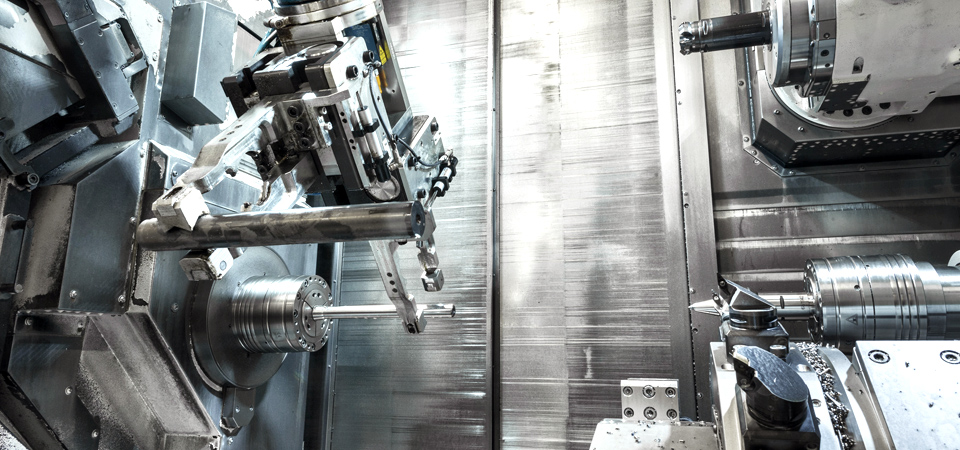
山特维克可乐满刀具生产工艺总监Lars Matiasson表示,该奖项的颁发为基默工厂带来了真正的自豪感,特别是在它认识到长期以来鼓励创新的努力已达到顶峰之际。“基默工厂的数字化之旅实际上始于30年前参数化CAD/CAM的实施。几年后,我们将其与智能自动化系统连接起来,从而在我们的生产中创建了第一个数字主线。这在很大程度上是一种发展,而不是一场革命。
“现在我们看到一个数字主线贯穿整个工厂,从库存管理一直到机器性能和预测性维护。这种创新精神始终是自上而下的承诺。基默工厂的总监和经理一直鼓励工程师以不同的方式思考并推动变革。最终,我们将着眼于如何利用技术提高工厂的效率和竞争力。这反过来又有助于实现可持续发展的未来。”
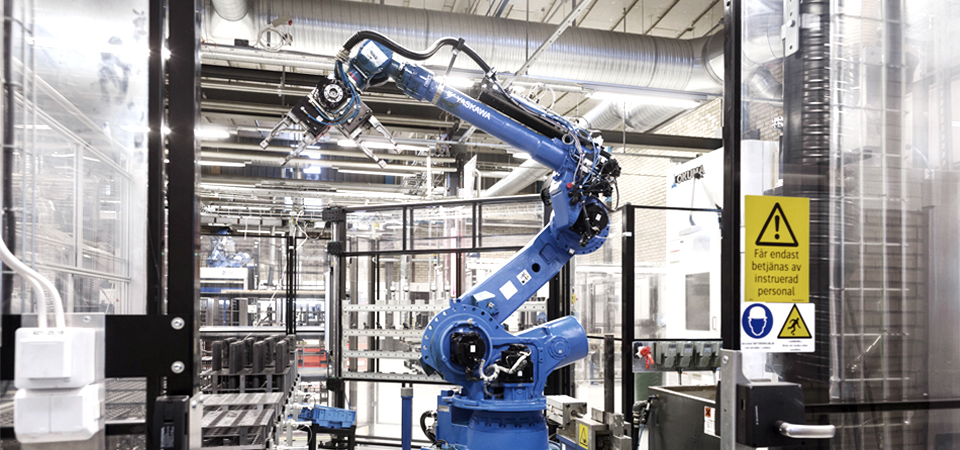
无接触转换就是一个很好的例子。在过去,必须手动更改生产单元的设计模式,操作员从白班开始就要准备好机床以便通宵运转。这需要时间和人力,而且在无人值守的轮班期间灵活性有限。另一种方法是投资于具有超灵活机器人、机床、刀具和夹具的智能自动化,它们可以一起完成复杂的无接触转换,而不需要任何人工监督。
Matiasson说:“大家关注的是诸如快速换模之类的精益生产技术,而我们想要走得更远。我们希望实现零劳动力装夹。”
“这是一段曲折的学习过程。第一个自动化单元并没有像我们希望的那样工作。实际上,它甚至不如一位操作员加一台机床的效率高。但这就是数字化问题 – 您需要不断地从失败中学习。渐渐地,我们取得了显著进步,机器人单元开始达到我们所需的效率。反复试验,不断摸索,这是确保实现改进的重要因素。”
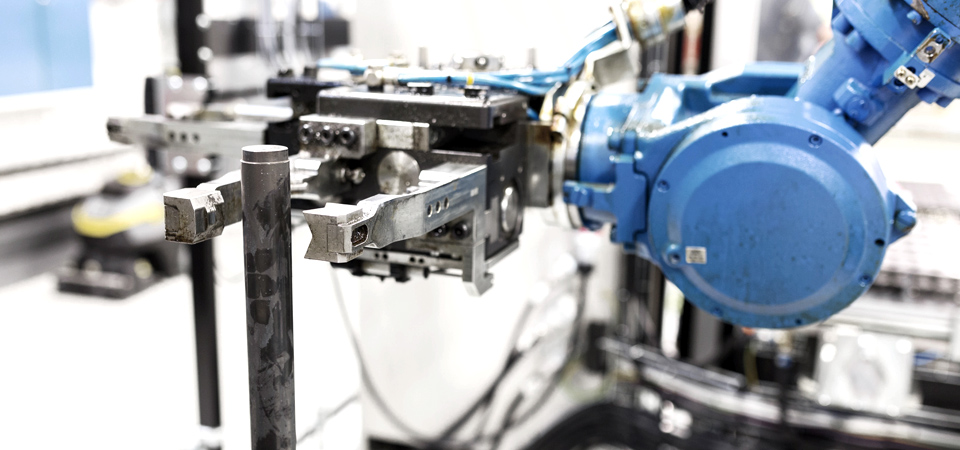
数字技术也用于在基默工厂的其他领域 (比如维护) 提供改进。越来越多的传感器被安装到工厂的各种设备上,围绕不断增长的参数列表收集数据,如压力、温度、振动和声学。这些数据与复杂的分析相结合,可以揭示模式和问题,避免发生停机。
工程师现在从整个生产设施收集数据 – 从机器人、数控机床,甚至从切削刀具自身。一旦提取并分析了这些数据,就可以对设备的运行状况提供有价值的见解。这些信息反过来又可用来预测和预防故障,从而提高工厂的效率。
山特维克可乐满也越来越多地将实时分析应用于生产环境,使其能够对机床进行更准确和及时的调整。“之后的阶段将是引进诸如人工智能和机器学习之类的尖端技术,机床可以从历史数据中学习,并具有自我控制的元素。这真是一个令人兴奋的领域。”
尽管有这些显著的技术进步,以及世界经济论坛的灯塔认可,基默工厂的数字化脚步从未停歇。