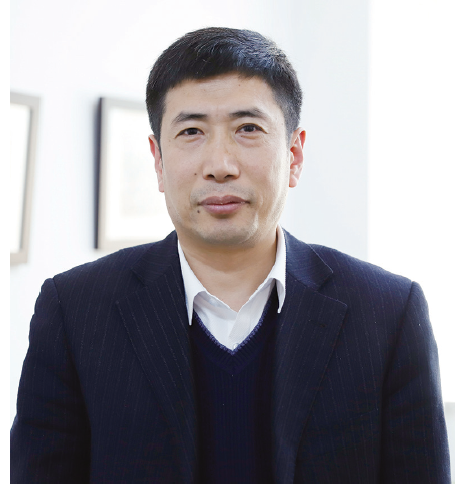
在“两化融合”和“工业4.0”的背景下,智能制造、大数据这些理念,越来越受到业界关注。刀具加工工艺作为制造业的重要环节,该如何更好地实现智能化,如何更好地借助大数据、云计算等前沿技术,实现高效的加工目的,也是亟待解决的课题。
此次,我们有幸采访到了王永国博士。作为上海大学先进工艺与刀具技术研究所的发起人,王永国博士可谓是中国刀具领域的“先行者”,其不仅对我国高端刀具人才的培养倾注了满腔的心血,同时也积极投身相关的产学研工作,在刀具加工工艺与切削大数据方面拥有丰富的实践经验。
王永国博士同时还是西安交通大学高端制造装备协同创新中心(2011)特聘教授,还担任“航空航天及汽车关键零部件加工工艺与切削大数据协同创新联盟”秘书长(理事长为卢秉恒院士)、先进制造工艺与刀具协同创新研发中心常务副主任(主任卢秉恒院士,投资1.43 亿)等职务,同时也与航空航天、汽车骨干企业、机床刀具等企业以及高校等机构建立了良好的合作关系。从理论与实践两相融合的角度而言,王博士此次的分享绝对是干货满满、不容错过。
智能化的重点和难点:加工工艺与切削大数据
王博士认为,加工工艺是机械加工中最重要的部分,加工工艺系统是指包含机床、工件、刀具、夹具和切削液在内的工艺系统;加工工艺优化也是针对这个工艺系统进行优化,以达到提高生产效率、提高产品精度和可靠性、降低加工成本的目的。就加工工艺而言,目前智能化的重点体现在“加工工艺与切削大数据”的建立,以及如何充分利用这个大数据优化工艺系统。
难点也是体现在“加工工艺与切削大数据”。国内有基于大量切削实验而建立的切削数据库,但由于切削实验时机床、工件、刀具、夹具和切削液等要素很难全部跟生产现场一致,造成实验室建立的数据库对实际生产的指导不够理想;另一方面,由于“加工工艺与切削大数据”的建立是一个系统的工程,前期投入产出不明显,国内用户基本没有建立加工工艺与切削的大数据。
对于如何解决这一困境,王博士也给出了自己的建议:一套完整的智能化刀具解决方案,应包含加工工艺与切削大数据、基于大数据的智能化刀具管理系统以及相应的专家团队。王博士尤其强调了专家团队的重要性,这是因为,随着传统制造向智能制造的转变,一方面由于企业技术人员忙于生产,很少有时间对加工工艺进行系统优化;另一方面,由于企业很难招聘到工艺优化的专家,企业的技术人员水平有限,应付正产生产可以,系统全面优化工艺有困难;即使企业能招聘到工艺优化的专家,由于需要专家解决的问题数量少,造成专家的利用率不高,专家对企业的成本太高。所以需要在国家支持下,建立加工工艺与切削大数据的专家团队,服务于行业。
协同创新是关键
在访谈过程中,王博士也多次强调切削大数据与加工工艺协同创新的重要性。对于现在不少刀具企业已经在做的数据采集工作,王博士也给予了高度评价,“这对提高刀具企业的整体水平以及企业核心竞争力很有帮助,刀具企业可以通过数据库进行技术积累,同时也可以更好地服务于用户。”
但同时,王博士也指出,只有企业参与是不够的,要推进切削大数据与加工工艺的协同创新,需要政府、用户企业、刀具企业和高校等全行业达成共识,充分意识到切削大数据与加工工艺的协同创新的重要性。政府要在政策上给予引导,比如加大对切削大数据与加工工艺的协同创新相关共性服务平台的资金支持;用户企业要给予切削大数据与加工工艺的协同创新机会,引入公共服务平台,同时让企业内部相关人员跟平台团队融为一体,以解决企业的问题为导向,同时制定建立加工工艺与切削大数据的目标和项目规划;刀具企业要跟用户企业和公共服务平台合作,在为用户提高效率、降低成本的同时,帮助用户建立加工工艺与切削大数据。
刀具智能化给国产刀具的发展带来契机
王博士指出,刀具智能化在整个制造业转型升级中发挥着关键作用,更重要的是,通过推广加工工艺与切削大数据,有助于在汽车和航空航天等关键行业大力推广国产刀具。
这是因为,制约国产刀具在汽车和航空航天领域使用的最重要因素不是寿命低,而是寿命不稳定,特别是汽车发动机等关键零部件行业,是以一批刀具中最低的一把刀具寿命作为这批刀具的寿命,而最低的刀具寿命可能是进口刀具寿命的十分之一,如果使用国产刀具,会严重影响用户企业的生产效率。
通过对加工过程中动态数据(如扭矩等)以及静态数据(切削参数等)的大数据分析,可以准确预测刀具的极限寿命,在不改变任何条件的前提下,刀具寿命可以普遍提高5-15%;依靠大数据的分析结果以及加工过程中动态数据的监控,可以使普通刀具具有智能化刀具的功能,在不出现废品零件的前提下,最大限度的提高刀具寿命。基于此前提下,只要国产刀具的平均寿命跟进口刀具相当,就不会影响用户企业的生产效率,从而解除了用户企业的后顾之忧。
对此,王博士还为我们讲述了一个具体的案例。之前,在高档数控机床与基础制造装备国家科技重大专项资金的支持下,王博士及其团队承担的国家科技重大专项“加工工艺与切削大数据”项目与重汽济南动力公司承担的山东省重点项目“发动机智能制造”成立了联合项目组,进行了一系列协同创新的尝试。重汽济南动力公司的刀具国产化,由课题开始时的不到10%增加到目前70%(2019年底将达到80%以上),实现了HSK整体式非标镗刀、焊接硬质合金铰刀、硬质合金钻头/铰刀、枪钻、整体硬质合金深孔钻、硬质合金涂层刀片/CBN刀片等系列刀具的开发,80%刀具达到或超过了进口刀具寿命,如项目组开发的精铰合金灰铸铁发动机缸盖φ26H7 2301/2306孔的焊接硬质合金6刃铰刀,刀具寿命是原进口德国知名品牌刀具的2倍,成本降低了60%。
大数据、软件和传感器将成为智能制造的三大基础
在访谈的最后,关于云计算、大数据这类前沿技术,如何更好地与传统制造业融合,王博士也和我们分享了来自卢秉恒院士、徐宗本院士的宝贵观点:
卢院士认为,智能制造新的三大基础:大数据、软件和传感器,海量的大数据要通过云计算才能指导生产,帮助传统制造业逐步走向智能制造。制造大数据的功能主要应包括:诊断装备运行状态,保障安全与质量;工艺过程控制,提升质量:如切削加工中的统计分析控制;优化工艺:集成多家用户的累积数据,得出工艺规律及用户工艺;评估制造装备的优劣、适用场合、装备薄弱环节,给出改进建议;制造资源的组织、优化。
徐宗本院士对制造业应用大数据的总体建议则包括:做好顶层设计,定准目标,选好切入点是关键,搭建统一化的制造业大数据平台;数据是基础,关联出价值,可以全面搜索、整理制造业营运及生产数据为切入点;培养好队伍,着力培养一批“懂业务、懂数据、会分析”的大数据人才队伍,保证大数据的可持续健康发展;形成独立自主的行业大数据技术,分析出价值;应以“内外结合、以己为主”的核心技术研发基地;协调推进大数据应用,解决好部门、层级间的应用需求与行业整体需求之间的关系;建立基于大数据应用决策的长效机制,强化组织体系建设 、统一数据标准、建立统一的数据收集、报送、应用制度。