整体叶盘5G解决方案是瑞典爱立信公司参与的5G欧洲计划创新项目之一。该方案为5G提供了明确的商业机会,以支持工业4.0。通过5G解决方案应对生产挑战,整体叶盘制造以及整个航空发动机行业都可以获得回报。
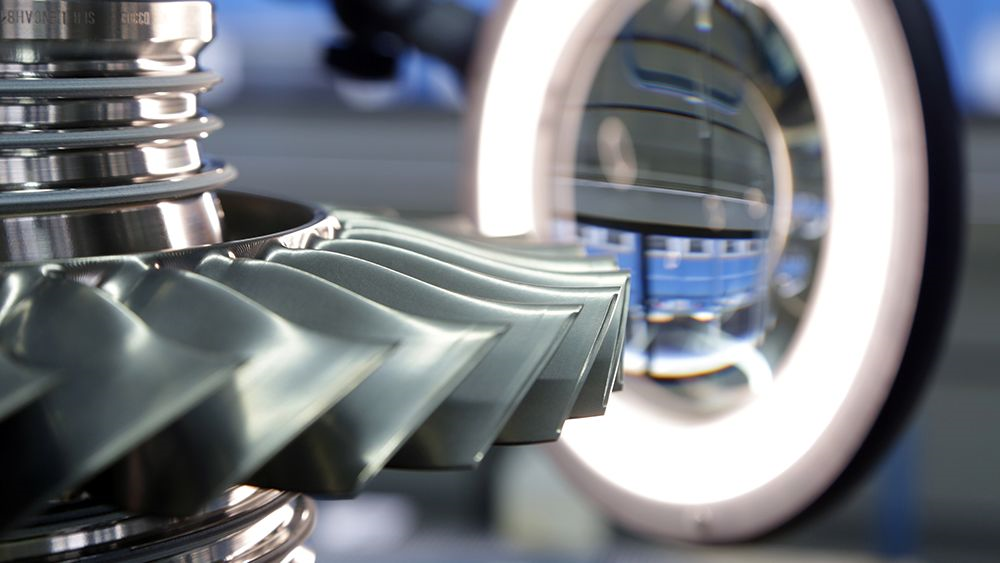
机遇
下一代工业生产力被称为工业4.0,工业4.0愿景包括以自动化,商业信息和制造系统为中心的包围技术,包括连接生产,其中所有组件都在自我管理系统中进行跟踪和配置。
移动通信和5G的引入可能成为工业4.0的重要推动者。允许工厂车间的连接和自动化以前所未有的规模改变制造业。
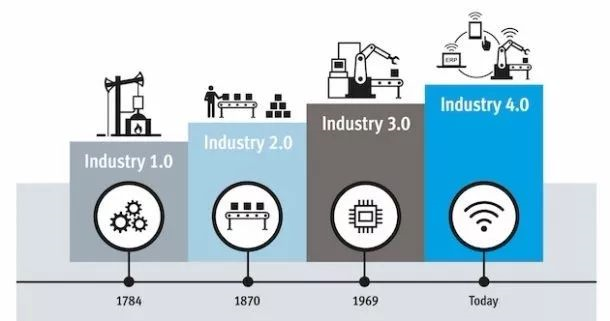
通过智能传感器和实时传输实现连接,有机会改善制造流程。仅这些技术的好处就证明在工厂中安装私有企业蜂窝网络是合理的,而且价值潜力巨大。一旦建立了5G网络,就可以实现真正的自动化工厂。可以通过一个标准化网络管理一系列连接的设备,如机器,传感器,材料和机器人,并根据需要分配正确的延迟和带宽。这是运营商最大的机会所在。
整体叶盘加工面临的挑战
对于最新的航空发动机部件,当涉及到满足系列生产过程中精度,部件安全性和效率的要求时,当今的生产技术已经受到挑战。特别是,如今的新型整体叶盘设计中的薄壁和高扭曲叶片需要极其稳定的铣削工艺和高度复杂的工艺规划,以避免在铣削过程中叶片振动而产生不可接受的表面缺陷,这使其成为整体叶盘制造中最关键的工艺流程。尽管当前的几何形状已经几乎克服了所有这些挑战,但未来的整体叶盘设计仍在不断发展,并且很快将超越当今生产系统的功能。
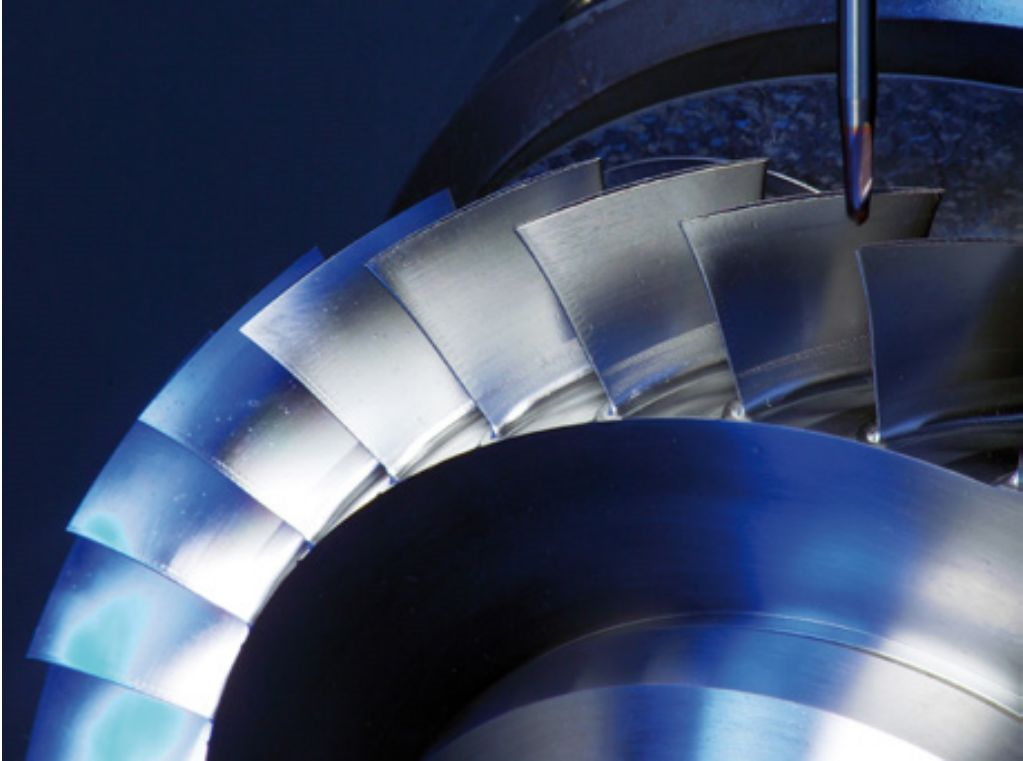
目前整体叶盘加工面临的一大问题就是加工过程很难监测其质量高,这意味着在切削完成之前不知道最终结果。目前整体叶盘铣削过程可以持续一整天甚至能够达到100小时或更长时间,并且返工率通常高达25%,总生产时间很长。因此通过实时监控过程可以发现铣削问题,例如影响最终结果的振动现象,然后,该数据可用于立即优化铣削过程,从而减少返工的次数。这种早期检测也将显著减少故障检测相关的成本。
解决方案
德国Aachen的Fraunhofer IPT于2019年开始与爱立信合作开发通过5G实现航空航天原型设计的自适应工艺设计。
Fraunhofer IPT项目测试了整体叶盘生产过程的自动化生产、监控和实时控制,通过向系统引入人工智能来识别可以进行改进的问题和领域。该项目设计了一个演示解决方案的成熟度模型,可以归纳为四个步骤:
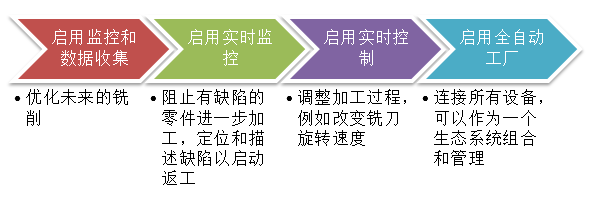
因为当前的4G技术不能支持这种解决方案,因此5G是关键。5G在这个案例中的主要优势是它可以提供非常低、稳定和可预测的延迟。对于实时控制,传感器的信息需要在1毫秒内处理和处理。5G技术可以通过提供这种低延迟功能来实现控制环路,从而使其能够在整体叶盘生产中应用。微型传感器和5G通信模块对于无线数据采集和此类情况的通信功能也至关重要。5G的引入还将带来更严格控制的监控功能,这意味着可以始终监控关键传感器(如整体叶盘振动传感器)的性能。
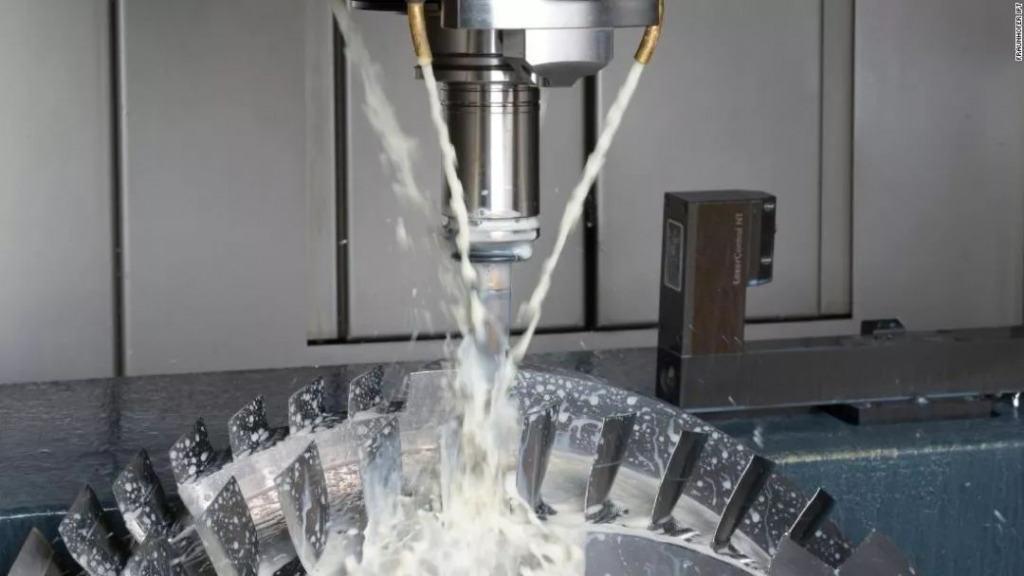
通过将直接使用5G的传感器放置在组件或工具上,爱立信能够实时检测故障并将错误率降低至15%。叶片的平均生产成本降低了3600欧元。
智能传感器技术
为一种新的叶盘几何体设计铣削过程的通常策略是基于反复试验,这种方法低效、耗时并依赖于工人的经验。此外,这使得该阶段的成本和持续时间更不可预测。
为了避免所有这些不确定性,IPT与爱立信合作采用的方法基于从智能传感器和机器控制系统收集的实时数据。结合工件模拟,该数据可以独特地了解切削刀具尖端与零件表面之间接触点的实际情况。
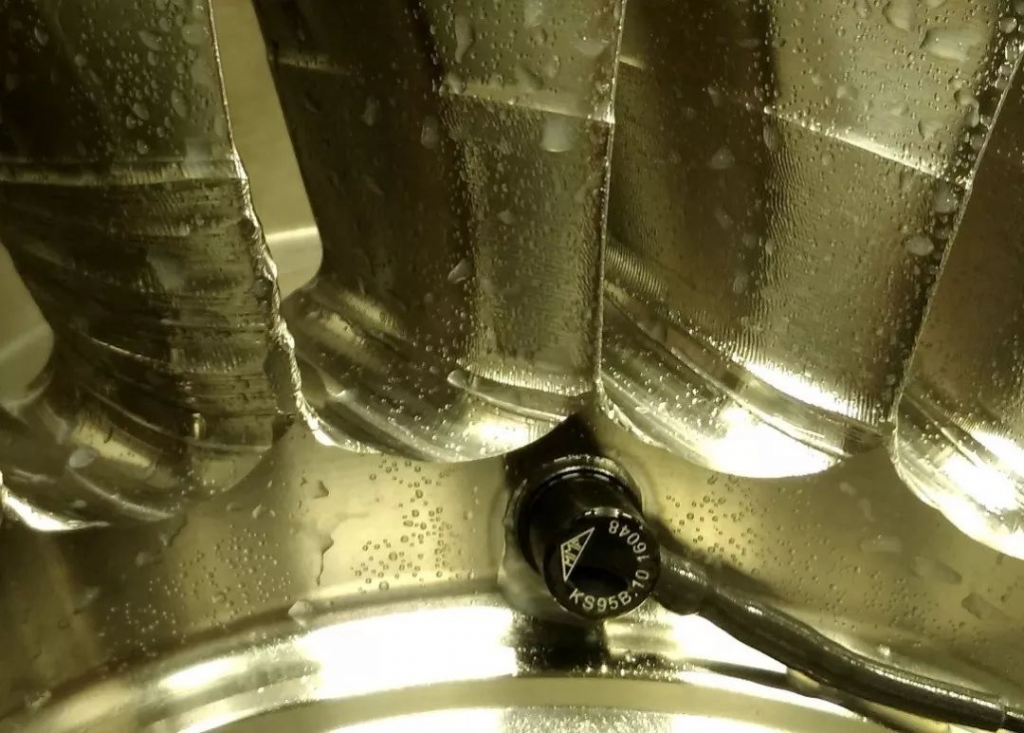
为了监控这个最重要的过程,工件本身配备了一个无线智能传感器,可以检测当前的过程稳定状态。该智能传感器使用直接连接到组件表面的微型加速度传感器捕获工件振动,如上图所示。用来监测以及无线5G传输的模块封装在IP68防水外壳中,可以在整个铣削过程中将整个装置放在铣床内并连接到工件上。传感器系统将频率范围高达10kHz的振动信号传输到机器外部的接收器系统,以进行后续数据分析和确定过程稳定性。
5G用于生产
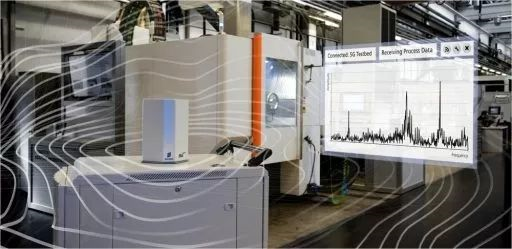
整体叶盘铣削项目是目前正在Aachen 5G装备的IPT车间进行的多项试验中的第一项,使用爱立信提供的全球生产环境中唯一的预商用5G系统。凭借5G设备和综合制造机械的独特组合,Fraunhofer IPT能够为各行业和研究领域的合作伙伴提供独特的测试平台,以实现众多工业无线应用。
自适应过程控制
在直接远程从过程获取振动信息之后,评估和处理是优化和稳定过程设计的下一个逻辑步骤,目的是为了让叶片不以共振频率(本征模式)状态工作。从机器的控制系统连续提取刀头坐标数据、传感器数据如今可以与工件表面上的工作位置相互关联。
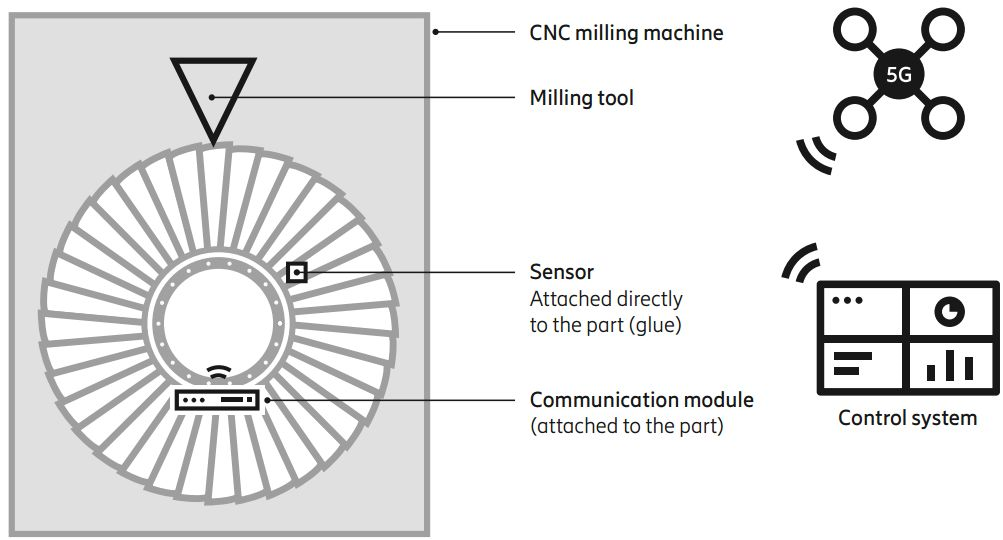
通过使用这种空间分辨的振动数据,结合叶片的模拟数据,可以导出精确定制的控制策略。从传感器的当前过程稳定性、机床控制的刀具位置和模拟数据作为输入,控制算法可以计算相对于实际工件状态及其不断变化的行为的最佳主轴速度。将此信息反馈给机器控制器最终形成闭环。利用模拟数据作为零件行为的背景信息,可以在检测到在线闭环控制时有效地避免振动导致中断发生的频率。
数字孪生和连接的整体叶盘
虽然过程监视和控制在制造过程中非常重要,但在CAD/CAM数据、制造数据和计量数据、运行数据和维护数据的整个生命周期内,纸质文档仍然是一项需要持续的工作。法律要求需要这些相关文档作为证明,这导致巨大的工作量,在大多数情况下,这些文档编辑工作由负责当前流程的工作人员手动完成。将数据连接应用于所有这些阶段,可以实现工业4.0最核心的下一个重要里程碑:将集成化的数据与所有联网客户端系统和用户可用性相结合。
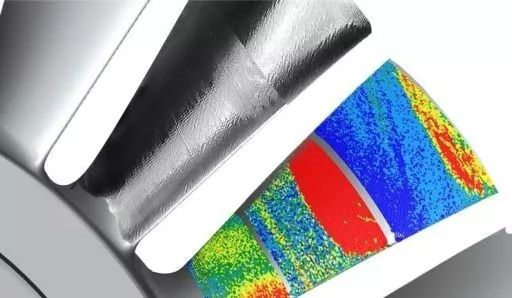
元件、系统或整个航空发动机的“Digital Twin”(数字孪生)组合了所有这些数据。该数据采集的自动化要求高度集成的传感器设备具有先进的预处理功能和通用无线数据接口。5G正是这个平台,一个适用于从低延迟传感器和控制应用到大批量长期统计数据采集系统的全球网络。
经济价值改善
整体叶盘生产经济性的潜力非常高,这个项目是在向工厂车间引入高性能连接时实现全新价值的一个有启发性的例证。今天整体叶盘的返工率约为25%,这意味着每4个整体叶盘中有1个需要重新加工。鉴于其高成本,返工率的任何降低都具有重要价值。如果通过自动化加工可以使返工率从25%降低到15%,则机器工作时间将减少,这可以转化为每个整体叶盘3600欧元机器成本的降低。
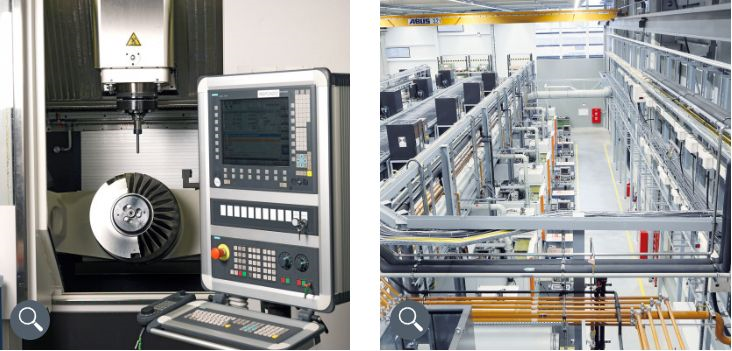
整体叶盘的市场正在不断增长。一家典型的整体叶盘工厂每天生产40个整体叶盘(包括返工),通过5G实现的实时监控和控制每年可节省2700万欧元。假设在全球范围内每年生产100000个整体叶盘,这意味着目前整体叶盘可以产生的额外生产价值每年约为3.6亿欧元,虽然这是一项重要的金属加工业务,但仍然只占全球金属加工总量的一小部分。
总结
改变娱乐、通信和交通的5G网络可能还需要数年时间,但在制造业,这项技术已经发挥了作用。下一代5G网络可以比4G快100倍,使设备和服务器之间的通信速度更快。这些网络可以十分便捷地安装在工厂等相对较小的区域。速度、实用性和潜在成本节约的结合促使工厂操作员尝试5G,其结果是积极的,这表明该技术可能会在智能手机和其他消费产品之前广泛用于工厂。
参考文献
[1] Ivana Kottasová. How 5G will transform manufacturing[OL] CNN Business. March 25, 2019.
[2] Paul Becker. 5G networked aerospace production[OL] Fraunhofer Institute for Production Technology IPT, Aachen. aero-mag.com. JANUARY 21, 2019.
[3] A case study on real-time control in manufacturing[Z] An Ericsson Consumer & IndustryLab Insight Report. April 2018.
[4] Denis Dilba. Blisk development: How blade and disk became one.[OL] aeroreport.de. 05.2019.
[5] 5G Open for Business – Ericsson presentation at the IEEE 5G and IoT Summit 2018 held at Thessaloniki, Greece on October 25, 2018.