Wagstaff,Inc。成立于1946年,是一家位于华盛顿州斯波坎的制造商,提供机械,技术和服务,使铝生产商能够将熔融铝转化为固体形状 – “方坯”(圆形)和“锭”(板坯)使用“直接冷却“铸造。直接冷硬铸造工艺使用水来冷却熔融铝,以便将其固化成所需形状,以便通过板材,板材,挤出,棒材和锻造零件制造进一步加工。在全球范围内,铝生产商希望Wagstaff获得安全铸造铝的专有技术和设备。
Wagstaff在斯波坎和肯塔基州的工厂开发,设计和制造复杂的模具,铸造机,自动化系统和辅助设备,并在迄今为止的58个国家/地区委托系统。凭借其广阔的工程部门和最先进的制造能力,Wagstaff为铝生产商提供创新,全面的解决方案,以实现铸造厂的最高质量和生产率。
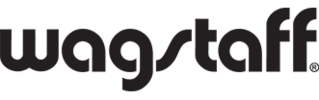
Wagstaff使用TDM的刀具生命周期管理来减少信息丢失并使车间运营更加出色
首先,一点背景:Wagstaff是铝行业的重要参与者,是设计和制造使用直接冷(DC)铸造方法生产原铝锭和方坯所需的系统和设备的领导者。他们的斯波坎工厂占地133,000平方英尺。并负责研发,制造,加工,装配,测试和运输。他们有大约30台CNC机床和20台非CNC机床。
但他们没有在一夜之间到达那里。这个美国的成功故事开始于1946年,位于乔治·瓦格斯塔夫(George Wagstaff)家庭住宅后面的一个泵房里。第一年,乔治,一位熟练的机械师,使用战争多余的车床为另一家机加工车间生产分包零件。白天,他在车床工作,晚上他在Kaiser Trentwood铝厂工作。随着时间的推移,他的辛勤工作得到了回报,使他能够购买第二台车床并扩展其加工业务。从那时起,家族企业一直在扩展。从20世纪60年代开始,在George的儿子Bill Wagstaff的领导下,该公司成为DC铝铸造技术的公认领导者。
Wagstaff的制造工程经理Jeff Smutny解释说,一家成长中的公司也面临着许多挑战。“在某个时刻,大约在2004年,我们意识到我们花了多少钱来处理丢失的信息。信息存储在特定产品线的过程文档中,一些信息存储在我们的CAM系统中,还有一些信息存在于Excel电子表格中。跟踪这些信息并将其用于新工作是很困难的。它只是效率不高,似乎每个人对特定刀具的使用方式都有不同看法。这花费了我们时间和金钱。“
Wagstaff的制造工程技术人员Russ Rasmussen很好地记得。“每个人都有自己的方式来处理信息,他们保持信息的不同。信息不一定在不同用户之间共享,”Rasmussen补充说。“例如,NC编程和车间之间的信息并不总是充分沟通。我们没有一个本地信息所在的数据库,因此它会被改变,克隆和变异。人们在二手信息上运行源信息。“
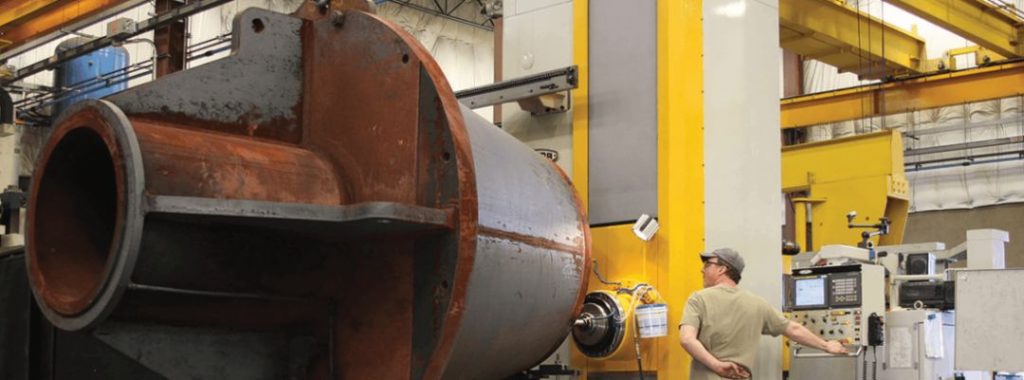
1提前准备需要的刀具数据
这种情况在2005年开始发生变化,当时Smutny作为Walter和Wagstaff当地Walter经销商的客人访问了德国的Walter总部。Smutny看到Walter在自己的商店中使用TDM System的刀具生命周期管理系统,他的范围和能力给他留下了深刻的印象。“我们的员工一直在考虑使用刀具预调仪,但数据管理实用程序很薄弱,”Smutny回忆道。“在看到运行中的TDM系统之后,很明显我们需要在获得预调仪之前获得一个刀具管理系统。”此外,他还指出,“Walter正在使用TDM与相同的CAD系统接口和相同的零件程序验证Wagstaff使用的系统。“
“刀具生命周期管理确保刀具数据在需要时随时可用,”TDM Systems销售总监Dan Speidel解释道。“它连接CAM系统,预置和婴儿床系统,以及CNC机床控制,但它也可以向上游扩展到规划和执行层面,如PPS,ERP和MES系统。为了扩展如此广泛的刀具生命周期管理系统必须是开放的,能够提供大量的导入和导出接口,并将来自各种来源的数据(例如制造商目录或内部创建的3D模型)集成到一个集中式数据库中。“
Speidel补充说,系统从生产中收集数据并将此数据传输到其他系统。刀具生命周期管理影响整个过程,从选择刀具到生产计划中的使用,到车间的无缝转移和使用。来自各个流程步骤的信息不断流回集中式数据库,从而创建可在整个网络系统中访问的大量数据。这是一个非常需要的系统。
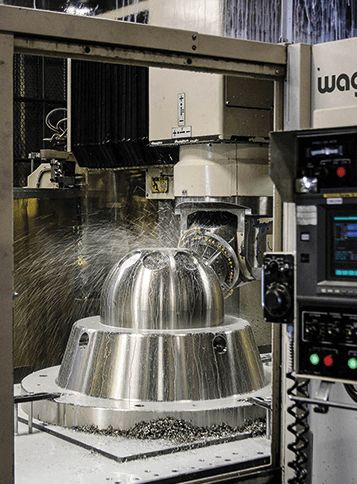
“Wagstaff拥有我们在众多公司中看到的典型的独立信息孤岛,”Speidel说。“旧的过程是找到一份工作并将其转交给工程师来设计和规划流程,然后将其转换为NC编程。一旦定义了NC程序,他们就会将程序移到刀具栏上并查看对于工作的刀具。他们会查看他们的藏品,机器操作员经常需要查看他的藏品。当然,每个人都有自己的刀具偏好。“ 它不一致也不高效。
“这家商店在各个地方都有很多刀具架,”Rasmussen说,“但是没有办法以数字方式搜索所有刀具,所以员工不得不四处走动搜索。中央刀具婴儿床主要削尖刀具,并试图维持库存水平。“
“他们到处都有刀具数据,”Speidel继续说道,“在Excel电子表格,Word刀具列表,刀具婴儿床索引卡,记事本,人们的个人驱动器,商店旅行者,机器刀具书或者只是头脑中关键在于没有中央刀具系统,这些信息不是数字可追溯或可搜索的。他们还有来自CGTech的Vericut来验证刀具路径,但该系统中的刀具信息未与CAM系统完全集成。 ”
这不是向Wagstaff扔石头,因为许多公司已经发现自己处于这个位置,不同之处在于Jeff,Russ和Howard Estes(现已退休)决心对此采取行动。他们的关键驱动因素是他们意识到他们需要在刀具信息方面变得更有条理,并利用数十年制造高度工程化产品所建立的丰富的部落知识。
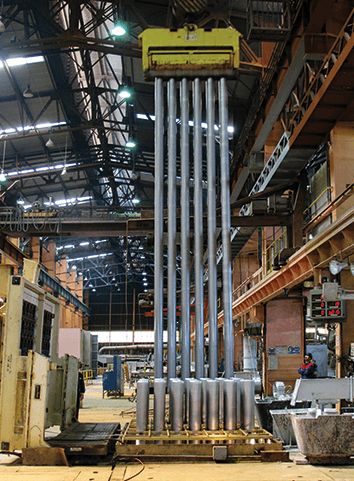
TDM刀具管理软件
2刀具生命周期管理
组织起来就是刀具的实际定义,这是刀具生命周期管理的第一步。对于Wagstaff来说,这不是一件容易的事,因为Rasmussen指出,“我们有大约4,000个刀具组件和许多更多的刀具组件。”
Speidel指出,公司经常满足于CAM系统的通用刀具模型,但要为此付出代价。他问过多少次,你看到程序员离开他们的办公桌,去商店寻找合适的刀具,或者去刀具栏询问,我们有类似的东西吗?如果您的NC程序员无法在访问数据库中搜索有关刀具栏内容的信息,那么他们必须站起来寻找有问题的刀具。结果:失去了时间。
刀具选择过程中会出现其他问题,例如哪些刀具最适合哪些工艺步骤?哪种组合最有效?TDM的刀具生命周期管理通过支持刀具及其潜在应用的基本信息,帮助Wagstaff快速回答这些问题。除了帮助每个NC操作选择刀具外,系统还可以存储每个刀具组件的几何和切削数据,使3D刀具图形可用于NC和模拟分析,并保存NC程序中的刀具列表以备将来使用。此外,切割数据,加工条件和最佳实践的记录允许在将来的应用中优化刀具使用。
“像这样的功能使得TDM在重复工作中获得了这样的好处,”Smutny说,“但它也会在新工作中发挥作用。例如,它可能是一个不同的产品或应用,但也许材料是相同的因此,程序员已经知道了使用这种材料的切削刀具和刀具组件的行为。总的来说,我们节省了大量的时间并且实现了精度的提高。”
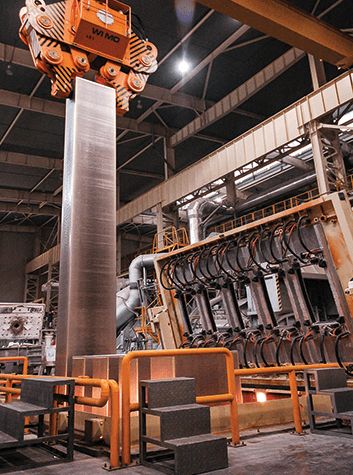
上面提到了刀具预调,TDM的刀具生命周期管理也带来了好处。TDM与领先的预调仪制造商合作,以促进双向通信。在测量过程中,这些系统可以访问存储在TDM系统中的每个刀具组件的标称数据,并将实际测量的数据传回TDM以不断微调系统。通过DNC或刀具芯片使用TDM执行该数据传输。刀具和NC程序同时到达正确的机器,以及预设刀具的当前实际数据,以及图形,照片和/或标题。Wagstaff最终购买了一台预调仪以补充TDM,但即使一家公司也没有.
访问准确的数据可以减少编程和作业设置时间,通常减少25%。“我们在刀具栏中有多达七个人。部分由于TDM,我们现在在三个区域运行该区域,”Rasmussen指出.Smutny补充道,“自从我们实施TDM以来,公司也发展了很多,但我们的编程工作人员的人员配置与2004年大致相同。我们现在花更多的时间准备创收工作,减少搜索信息的时间.TDM增加了我们的带宽。“
拉斯穆森继续说道:“跟踪我们大约4,000个刀具组件和刀具组件过去是一件令人头疼的问题,并消耗工时,否则可以用于增值活动。”现在我们知道我们需要库存的是什么切割刀具,扩展,持有人,夹头,你的名字,所以这肯定简化了购买功能,除了减少库存“他补充说。充分了解Wagstaff的刀具和这些刀具的功能使公司减少他们的购买在某些地区。
他承认,对新系统的支持不是自动的。“人们不喜欢采用新事物,因此总会有一定程度的犹豫。然而,今天情况却不同。我们的一位程序员最近向我提到他不知道如果没有TDM他是如何完成工作的。它已成为我们成功运营的重要组成部分。”
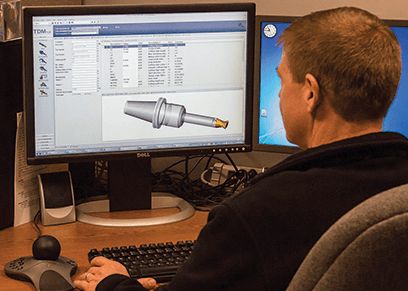
我们现在可以花费更多的时间和精力在准备创收的工作上,而不是浪费在查找刀具上面,TDM让工作更高效。
工艺工程师